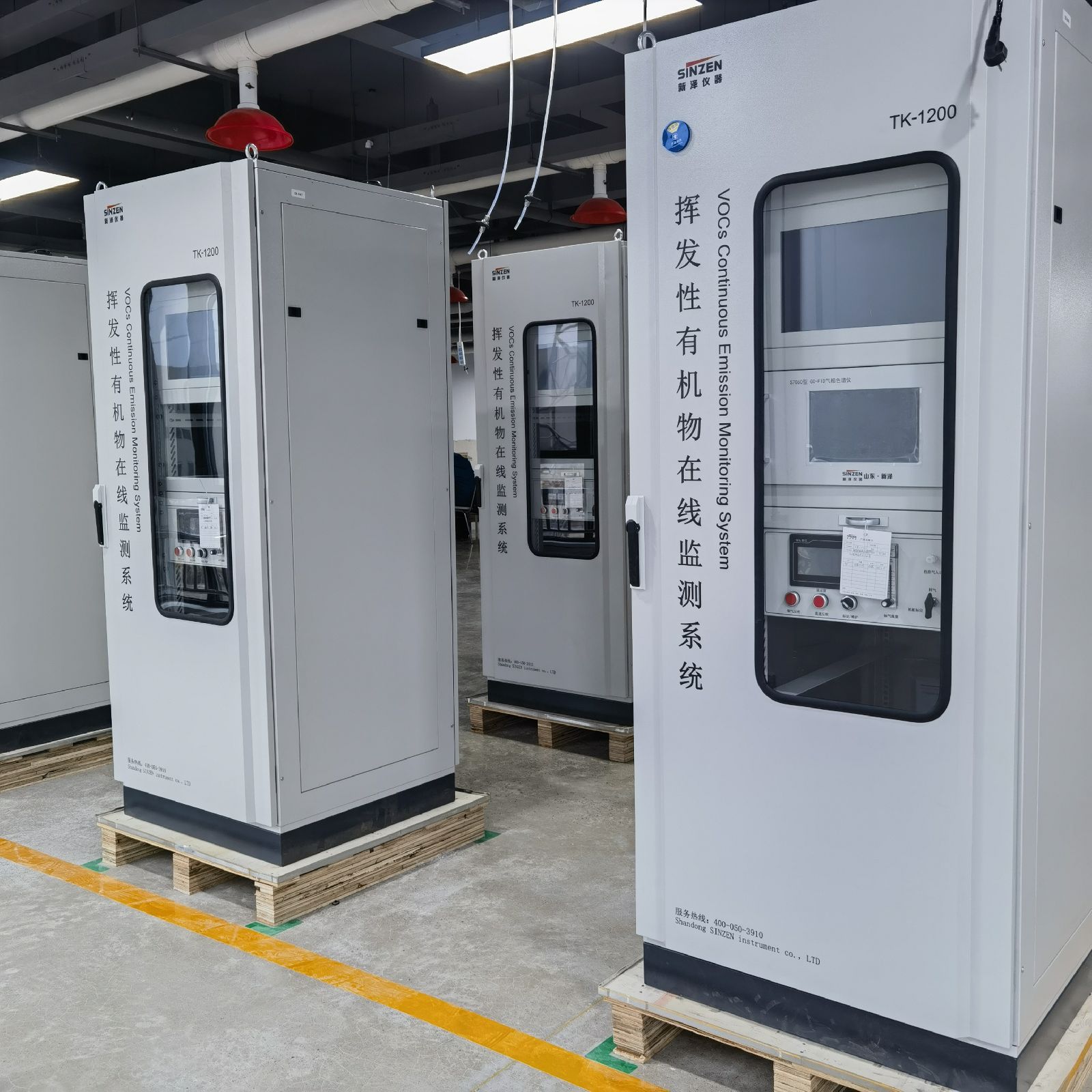
在工业有机废气净化领域,RCO(蓄热催化燃烧)、CO(催化燃烧)、RTO(蓄热燃烧)是三种常见的处理技术。它们各自具有独特的原理和特点,适用于不同的废气处理场景。
一、基本原理
RCO:利用VOCs氧化催化剂的作用,催化氧化有机废气中的VOCs,同时利用蓄热体的蓄热能力对VOCs氧化反应产生的能量和加热设备产生的热量进行循环利用。
CO:原理是通过催化剂的作用,将有机废气中的VOCs在较低的温度下氧化分解为二氧化碳和水。
RTO:原理是在高温下将废气中的有机物(VOCs)氧化成对应的二氧化碳和水,从而净化废气,并回收废气分解时所释放出来的热量。
二、优缺点分析
(一)RCO工艺
优点
操作温度低,一般在250-400℃,相比RTO的高温操作(800-1000℃)更节能,同时热回收效率高(>90%),运行成本较RTO低。
高去除率,对VOCs的去除率可达到95%~99%。
缺点
催化剂易失活,遇到含硫、卤素等化合物时容易中毒、烧结、结焦,影响催化活性。
陶瓷蓄热体床层压损大且易阻塞。
处理含氮化合物时可能造成烟气中NOx超标。
常用贵金属催化剂成本高,增加了投资成本。
有废弃催化剂处理问题。
不适合处理易自聚、易反应等物质(如苯乙烯),其会发生自聚现象,产生高沸点交联物质,造成蓄热体堵塞。
不适合处理硅烷类物质,燃烧生成固体尘灰会堵塞蓄热陶瓷或切换阀密封面。
(二)CO工艺
优点
操作温度较直接燃烧(TO)低,一般在250-400℃,运行费用相对较低。
相较于TO,燃料消耗量少。
处理效率正常在80%-90%之间。
缺点
催化剂易失活,遇到含硫、卤素等化合物时容易中毒、烧结、结焦,影响催化活性。
常用贵金属催化剂价格高。
有废弃催化剂处理问题。
处理低浓度VOCs时燃料费用高,经济性较差。
(三)RTO工艺
优点
热回收效率高(>90%),运行费用低。
净化效率高,对VOCs的去除率可达到95%~99%。
适用于高温气体,在处理高温废气时具有一定的经济优势。
缺点
陶瓷蓄热体床层压损大且易阻塞。
低VOCs浓度时燃料费用高,运行成本上升。
处理含氮化合物时可能造成烟气中NOx超标。
不适合处理易自聚化合物(如苯乙烯等),其会发生自聚现象,产生高沸点交联物质,造成蓄热体堵塞;不适合处理硅烷类物质,燃烧生成固体尘灰会堵塞蓄热陶瓷或切换阀密封面。
三、应用建议
RCO:适用于中高浓度的VOCs废气处理,尤其在对运行成本较为敏感且废气成分相对稳定的场景中具有优势。但在选择RCO工艺时,需充分考虑废气中是否含有对催化剂有毒害作用的物质。
CO:适用于VOCs浓度相对较高且较为稳定的废气处理,可作为一种高效的净化手段。但在处理低浓度VOCs或含有对催化剂有害物质的废气时需谨慎选择。
RTO:适用于处理VOCs浓度较高、废气流量较大且具有一定热值的废气,特别是在对净化效率和热能回收有较高要求的场合。然而,对于低浓度VOCs废气或废气成分复杂、含有易导致蓄热体堵塞物质的情况,需要进行详细的评估和预处理设计。
总的来说,RCO、CO、RTO三种废气处理技术各有特点和适用场景。企业在选择时应根据自身的废气性质、浓度、流量以及成本预算等多方面因素进行综合评估,以确定*适合的废气处理工艺。